Custom apparel printing has changed the game in self-expression, branding, and even event promotional marketing. From family reunions to sports teams, designing custom t-shirts for various occasions and businesses custom printing is most definitely the way to go.Custom printing has emerged as a solution to the need for quality apparel for individual and corporate wear. With an upward increase in the demand for clothing, the customization trend will only continue to grow, along with the technology and procedures needed to achieve that, including printing techniques which all have distinct advantages and features.
One of the best mentioned will be Kasparov’s and Benson’s printing sounded making waves in the customs world are DTF (Direct-to-Film) Transfer and Screen Print Transfer. However, if you do decide to opt for one or the other then you need to know the advantages and disadvantages of these two methods. What makes them so different is the level of designs they can take, the method of application and the cost, however. In this comparison, we study these two printing methods that are effective on creating durable and colorful garments.
Essential Equipment for DTF Printing: A Beginner’s Guide
What is DTF Transfer Printing?
The DTF (Direct-to-Film) printing involves a transfer process where prints are directly adhered to fabrics from a film that has been specially manufactured for the purpose. These are the stages of the DTF procedure in further detail:
- Design creation: In computer graphic development, quite a specific image and in its essence a way in which it is possible to reproduce oneself is used. Through this digital, printing output of careful details and bright colors becomes possible in the end.
- Printing on the film: The film designed for DTF printing, PET (Polyethylene Terephthalate) is printed with a designed image. In order for colors to stand out against many different fabrics, white ink is placed as the last coat of ink on the surface.
- Powder application: Once the inking process is accomplished, the finishing powder is sprayed on the wet ink on the film surface. This particular powder acts as the ‘glue’ which possesses the capability to bond the prints when applied to fabric.
- Curing the powder: Then the heat curing process is performed on the film coated with powder adhesive to ensure fixing of the adhesive powder on the surface and makes it ready for the design transfer application stage.
- Heat Transfer: In the last stage of the process, the film is applied to the fabric to be printed and heat pressed. Under the application of pressure and heat to the used powder coated surfaces, the ‘paste’ becomes liquid bonding the fabric and the powder permanently.
- Peeling of the film: When the fabric has cooled down for a while, the film can be removed with ease and the desired image of high resolution appears on the cloth.
Key Features and Benefits of Using DTF Transfers
- High Quality Prints: DTF transfers are resolute which enables transferring high resolution and colourful design even onto dark colored fabric.
- Various Types of Fabric Can Now be Used: DTF aids in printing a variety of materials like cotton, polyester, blends, nylon and so on making it suitable for various garment styles.
- Easy on the Eye and Sturdy: Another prime attribute of DTF prints is its easy soft and flexible touch which doesn’t crack or peel too easy thus making it comfortable for the end user as well as making the garment sturdy.
- Economical for Limited Batches: DTF is cost efficient for limited orders is different from trade screen printing options as much of the expenses incurred in initial setup are not incurred.
- Very Good Washing Lights: Garment production is enhanced as DTF prints can wash meat with fading, grazes and peel-offs especially after excessive wash.
- Good Alternative: In comparison to some alternative techniques of printing, DTF is more environmentally friendly may use less water and produces less waste.
These characteristics help explain why custom apparel printers seeking quality and durability across a wide variety of fabrics prefer to use DTF transfers.
What is Screen Print Transfer?
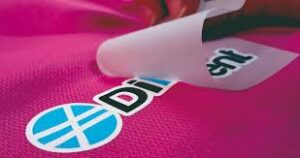
Screen Printer can also be referred to as silkscreen or serigraphy in other countries. As far as general practices are concerned, this form of fabric printing is focused on the physical placement of ink onto materials with the help of a stencil. Let’s see how the screen printing process is carried out:
- Design Preparation: Each design is disassembled by color and colored parts into single stand-alone stencils.
- Creating the Screens: The transfers are then burned onto the screen mesh along with emulsion light, which Is covered in light sensitive emulsion. Portions of the screen that do not form part of the design are sandpapered, effectively making a stencil.
- Setting up the Screen and Ink: The screed was pulled down so it was in contact with the fabric and attached above the fabrics was a screen stencil with swathes of ink, squeegeed through the unblocked areas.
- Layering Colors: In multi-colored decorations, each screen depicting a different colour is adjusted and applied in that order of use, each layer being dried first before the subsequent one is added.
- Curing the Ink: The last stage takes place after all colors have been applied, after which the fabric is passed through curing which is said to set the ink and incorporate wash fastness.
Screen printing is a popular method for creating designs on various materials, especially for large batches.
Key Features and Benefits of Using Screen Print Transfers
- Vibrant and Long-Lasting colors: After many washes, the colors employed in screen print transfers remain bright and do not fade.
- Ideal for High-Volume Production: It requires little time and money in the context of large quantity orders which leads to its widespread use.
- Thick and Opaque Coverage: Usually screen printing inks are thicker which results in deep bold colors that can be used on dark material.
- Variety of Ink Types: Screen printing makes it possible to incorporate effective ink such as glitter, metallic, puff, glow-in-the-dark, and other unusual finishes.
- Strong and Washable Prints: Cured screen prints are strong enough to be washed time and time again without any considerable fading or cracking.
- Economically Advantages for Basic Designs: Basic designs with one color logo can be printed by screen printing at a low cost more so for bulk orders.
These benefits make screen printing a reliable option for producing long-lasting, vivid designs on custom apparel, especially for large runs and high-demand items.
Comparing DTF Transfer and Screen Print Transfer
Cost Analysis: Initial Investment, Per-Unit Costs, and Value Over Time
- DTF Transfers:
- Initial Investment: Moderate to High. Requires specialized DTF printer, curing oven, PET film and adhesive powder.
- Per-Unit Costs: More expensive for small runs since all prints need film and powder.
- Value Over Time: DTF is economical for lower quantities or multi design orders as there is no expensive setup. However, for high volumes of production, the cost per unit is not low against screen printing.
- Screen Print Transfers:
- Initial Investment: Moderate. Needs a basic screen printing setup with a screen for every color and inks.
- Per-Unit Costs: Total Cost is Low for large orders as it gets shared across multiple batches owing to screens which can be used again.
- Value Over Time: Very reasonable for bulk orders. Though, the initial setup cost is high, it is cheap for high volume orders because of a lengthy variation.
Quality of Prints: Durability, Vibrancy, and Resolution Comparison
- DTF Transfers:
- Durability: Exceptional. DTF prints can be subjected to numerous washes and still retain their original feel without having cracks or stamps peel off.
- Vibrancy: High level of color vibrancy achieved even when printed onto dark materials.
- Resolution: High resolutions when printing designs which have numerous colors and details which makes DTF well suited for different complex images.
- Screen Print Transfers:
- Durability: Very durable too especially after curing. Several washes can be done but with time, the ink might fade.
- Vibrancy: Bright sunsets and bold opaque colors on black materials, but the minute differences in color tint that DTF is able to attain are less in comparison.
- Resolution: Better suited to basic patterns that are attention-grabbing. Small and fiddly details may be more difficult due to the restrictions of mesh screens.
Material Compatibility: Types of Fabrics Suitable for Each Method
- DTF Transfers: These can be used on a wide range of fabrics such as cotton, polyester, blends and other synthetic materials since the adhesive works on various fabrics.
- Screen Print Transfers: Effective generally on cotton and cotton blends, synthetic fabrics may sometimes not hold the ink well, and fabric types like nylon may need some modification.
Production Speed: Time Taken for Setup, Printing, and Curing
- DTF Transfers:
- Setup: Quick and easy, in particular for single designs.
- Printing and Curing: Average time; post-printing film needs to be cured which spans a little time.
- Total Time: Time-saving for small & medium size orders but time compounding in the case of larger orders because of curing.
- Screen Print Transfers:
- Setup: Lengthy since the screens are prepared for all the colors in the design.
- Printing and Curing: Very fast turnaround especially for large quantity orders after the setup is done.
- Total Time: Bulk orders after setup are completed as they are quick for screen printing however screen printing is not very efficient for single or small orders.
Complexity of Designs: Best Use Cases for Intricate Designs or Multiple Colors
- DTF Transfers:
- The method of choice for voted graphics artists for creates with complex shapes, multi-gradient hues, shadows and multiple range colors because the resolution and the number of colors are very high.
- Suitable for lower quantities that require complex graphics consisting of many colors.
- Screen Print Transfers:
- More suitable for bright and simple graphic designs that are not complex as each color requires a separate screen during printing.
- Most suitable for high-volume orders in which logotypes and brief messages are printed or any trace out of graphics is used which does not require large quantities of details.
Pros and Cons of DTF Transfer
Advantages of DTF Over Screen Printing
- Higher Detail and Color Range: DTF printing allows for intricate designs with many details and colors whereas other methods like screen printing require multiple different screens. This makes DTF not only suitable for the professional arena, but also for images containing fine details, small text, and multi colored artwork.
- No Limit on Order Size: With DTF prints, there us no minimum order quantity, which is especially beneficial for short runs or for one-off prints. Whereas, screen printing, will only become profitable for large volumes.
- Versatile Fabric Compatibility: DTF is best suited for a variety of fabric types, including cotton, polyester, blends, and synthetic materials such as nylon. On the other side, screen printing has limitations to cotton and cotton blends, and some synthetic fabrics may need special adjustments.
- Soft, Flexible Prints: DTF prints are soft to the touch and stretchable which is particularly useful for stretchy fabrics or comfortable clothing. In contrast, screen printing can sometimes produce heavier and stiffer feel on the fabric.
- Faster Setup and Turnaround for Small Orders: Compared to screen printing that involves setting up a screen for each color, DTF is much easier to set up. As a result, DTF is more suitable for rush orders.
- Green Alternative: Many consider DTF eco-friendly because it avoids ink and extra screens for every design. This is particularly the case when it comes to small runs which in screen printing setup waste can be relatively high.
Limitations or Challenges Faced with DTF Transfers
- Increased Cost Per Unit with Size: Although DTF is suitable for small orders, the unit cost for larger orders is still higher than that of screen printing. Unfortunately for DTF in large orders, the screens for screen printing are reusable and significantly reduce costs for bulk production.
- Need for Special Equipment: There is a specific printer, PET film, adhesive powder, and curing equipment used to print DTF designs. Such an exclusive arrangement may be expensive to set up and may not be available to every printer.
- Possibly Bonding Problems: The bond between the design and the fabric in DTF transfers is created using adhesive powder. The bond may not be strong if it is not well applied or cured, leading to adverse effects on the longevity of the design.
- Waste of Film: Since a new piece of PET film is required for every DTF print, it contributes to a great deal of wastage especially if the number of prints or orders is low. Although the method is environmentally friendly in terms of water usage, the waste of film can be considerable.
- Thicker Coating Process is Longer: In DTF, Curing is an important aspect which takes a lot of time especially in cases of bulk orders. Failing to render this stage properly or hurrying through it compromises the strength of the print and the designs can start cracking or pealing with time.
- Not Suitable for Big Designs: For example, a significant DTF print can be seen on a large design that covers a big area of fabric. This could have an impact on the comfort level and breathability of the fabric for certain clothing.
When it comes to detailed designs, smaller orders, and various fabric types, DTF transfers provide good versatility and quality; however, they are a bit more complicated since they require specific equipment and management as opposed to bulk screen printing’s simplicity.
Pros and Cons of Screen Print Transfer
Advantages of Screen Printing Compared to DTF
- Cost-Effective for Large Orders: Once the screen riggings are done, there is quite a low cost attached to repeated preparing for the same print thanks to the very quick setups required. This justifies the bridge in the production of many identical designs at once.
- Vibrant and Opaque Colors: Thr screen printing inks have a thicker and clear base resulting into creation of a deep and saturated colors which are capable of being visible even against dark fabric. Yet such intensity can become troublesome when using some DTF prints when designing on darker prints just the contrary of screen prints.
- High Durability: Cured screen prints are quite durable and especially for a simple design. They retain their quality and do not peel off or crack even after numerous washes which makes them suitable for long lasting wear.
- Specialty Ink Options: DTF is limited by the fact that he cannot provide a metallic, glitter, puff or glow in the dark ink which makes screen printing offer a heads up when talking about effects of the colors on the designs. Such variety of special inks adds to the creative freedom in design that DTF is unable to provide.
- Efficient Production Speed for High Volumes: screen printing in large quantities because, in many cases, the same pattern has to be made many times. Once the setup is complete, it takes a little time to prepare for mass printing so the same design can be printed over several hundred or thousands of items without breaks.
- Simple and Eco-Friendly for Basic Prints: One more method of printing which utilizes thickness is the creation of a stencil cut out of a mesh with ink applied to it, suitable for more straightforward designs that require just one color.
Limitations or Challenges Faced with Screen Printing
- Time-Consuming Setup: Each of the colors used in a design requires a separate screen, which requires making it, aligning it and then preparing it. This setup can also be time consuming and is moreover, uneconomical for small orders or designs with many colors.
- Limited Detail and Color Complexity: Because of mesh screen and ink application limitations, screen printing does not fit well with complex designs, color transitions or pictures with a great deal of detail. The process of making fine detail and images of photographic quality is easily one of the more difficult aspects in screen printing.
- Higher Initial Costs for Small Batches: With screen printing, many runs prove to be less economical. The setup costs however are fixed and do not vary with the order size creating an unsustainable cost for small quantities or custom orders.
- Limited Fabric Compatability: Best fabrics for screen printing are pure cotton or cotton blends. Certain synthetic materials such as nylon or stretchable fabrics can pose some challenges as the proper ink adhesion is hard to achieve without special inks or alteration in the inks.
- Environmental Concerns with the Use Of Inks and the Screens: Conventional screen printing processes tend to waste more materials especially unused inks and the water needed for water washing screens. Some inks such as plastisol are also considered environmentally hazardous and require some chemical cleaning agents.
- Storage and Screen Maintenance: Screens occupy some space and they must be properly stored and handled. Once a design is no longer used, the screens have to be washed and reclaimed for other designs which further add to the overall labor input involved in this process.
Among the techniques available, screen printing is perhaps the best option for large, simple prints requiring uniform colors and extended durability. On the other hand, it has limited use in intricate designs, small volume runs, or if soft touch prints are required – here, DTF might be more beneficial.
Best Applications for Each Method
Ideal Scenarios for Using DTF Transfer Printing
- Small Orders or One-Off Prints: DTF is very economical when it comes to low volume or a single print due to its low setup costs. This makes it ideal for special requests, print on demand, and personalized products.
- Complex, Multi-Colored Designs: DTF does a great job at reproducing complex multi-color designs consisting of gradients and finer details. It is perfect for complex graphic designs or images which require high definition and precision of colors.
- Varied Fabric Types: DTF transfers can be applied to a wide assortment of materials, for instance, cotton, polyester, blends, and synthetic fabrics such as nylon. This feature enhances DTF to print also on combined materials or unconventional fabrics.
- Fast Turn Round for Custom Orders: DTF does not have extensive setup procedure hence is suitable for fast and spontaneous orders. This is an advantage for businesses or individuals who require prompt delivery of customized designs.
- Soft and Flexible Prints for Comfort: DTF transfers give out a flexibility and softness feel which makes them appropriate for clothing items with high comfort like t-shirts and sportswear.
- High Wash Durability Prints: DTF transfers provide above average wash ability and flexibility durability, hence are of great use for garments which require constant washing such as sport kits or children outfits.
Ideal Scenarios for Using Screen Print Transfers
- Bulk Orders with Straightforward Designs: Bulk orders using the same designs in many different items such as a company logo, team uniforms or promotional shirts are well served by screen printing bulk orders.
- One or Few Colors: Embroidery or screen printing is also suitable due to its high efficiency for designs which consist of one or few colors. Common examples include logos, simple drawings or phrases.
- Lasts a Long Time: The technique provides great quality prints which do not fade. Therefore it is ideal for printing uniforms, work clothes, or other items that will be frequently laundered.
- Special Effect Inks: The other complementary advantage of personalized printing is the use of unique screen printing specialty inks metallic, glitter, puff, glow in the dark etc., that creates fantastic effects on designs that require such textures.
- Printing large black designs: When printing large black designs on tote bags or even large T shirts, hoodies or banners, this method screen printing method provides a thicker opaque coverage. For projects that require a large area to be covered with a bold or solid colors, this technique is ideal.
- Eco-friendly Simple Designs: If these graphics are already prepared for printing, most of the processes can be fully automated, meaning low waste when efficiently managed in large volume orders.
In summary, the DTF serves quite well for an order of small-size and custom made having a complex design with more fabric options while forth printing serves best for bulk-order with simple design those need durability & vibrance with low-cost.
Conclusion
In the world of custom apparel printing, DTF and screen printing both serve unique roles with distinct advantages and limitations. Understanding each method’s strengths helps businesses and creators make informed decisions that align with their project’s goals, design complexity, and production scale.
Recap of Main Points Discussed
- DTF Printing:
- Most suitable for small orders, complex graphics, and multiple fabric types.
- Prints intese, soft colors with no minimum order quantity.
- Needs specialized equipment and can be expensive for bulk quantities.
- Screen Printing:
- Most efficient for mass production, cheaper designs, and high strength level.
- Economically efficient when ordered in bulk accompanied by bright colors and specialty inks.
- Time requiring to set up, and the technique is not appropriate for single order detailed & multicolor designs.
Final Thoughts on Choosing the Right Printing Method
Using DTF technology, it is possible to print on all fabrics and to implement any graphics or designs for one-off, custom, or highly intricate projects – and that is its strong advantage. Simplicity of form and abundance of color are efficiently and economically delivered by screen printing for large print runs.
All things considered, the right method relies upon the dimensions, intricacy, and type of fabric of the apparel in question. Taking these elements into account will enable you to choose the best way of producing durable personalized clothing.